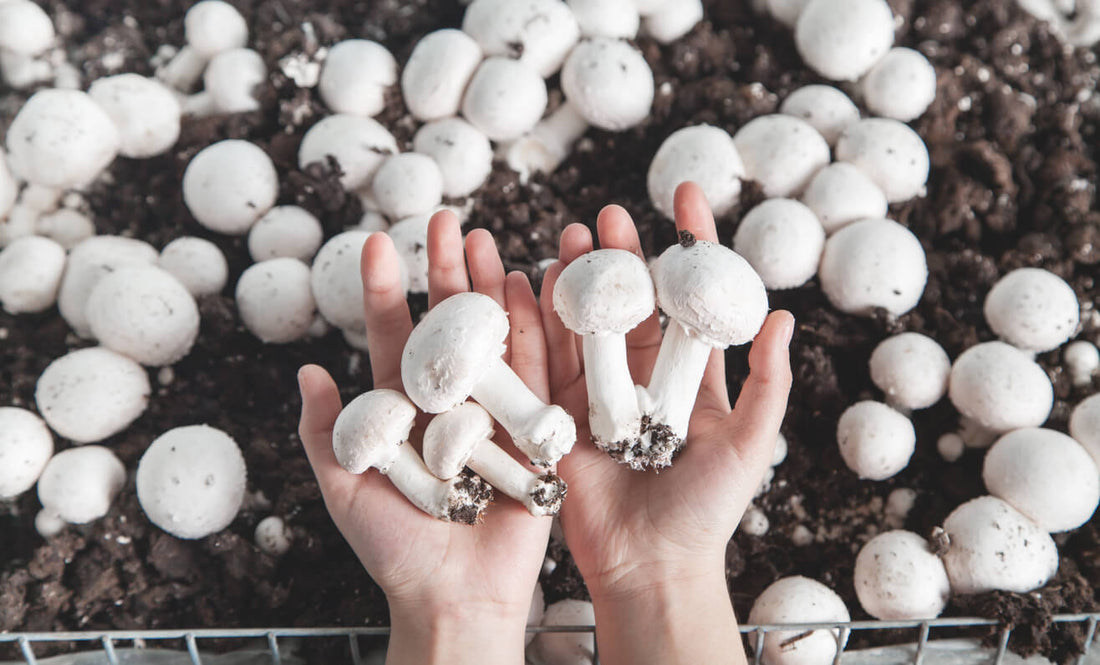
How to Scale Mushroom Substrate Production for Commercial Use
Share
How to Scale Mushroom Substrate Production for Commercial Use
Scaling mushroom substrate production for commercial purposes is a critical step for any grower looking to expand operations and meet increasing market demands. Whether you're a small-scale farmer looking to grow your business or an established commercial producer, understanding the intricacies of scaling is essential. This guide will walk you through the key considerations, methods, equipment, and safety precautions necessary to scale your mushroom substrate production effectively and sustainably.
Key Takeaways
- Scaling mushroom substrate production is essential for meeting market demand and increasing profitability in commercial operations.
- Different scaling methods—manual, semi-automated, and fully-automated—offer varying levels of efficiency, control, and resource investment.
- Critical factors in scaling include choosing the right raw materials, optimizing growing conditions, and implementing proper equipment for sterilization, mixing, and packaging.
- Safety precautions and adherence to regulations are vital to maintaining production integrity and protecting personnel.
What Is Mushroom Substrate Production?
Mushroom substrate production involves creating a nutrient-rich medium that provides the necessary environment for mushrooms to grow. The substrate is typically composed of organic materials like straw, sawdust, wood chips, or compost, which supply the essential nutrients, moisture, and structural support needed for mycelium development and mushroom fruiting.
In commercial settings, mushroom substrate production is a meticulously controlled process that ensures the consistency and quality required for large-scale cultivation. The choice of substrate material is influenced by the type of mushrooms being grown, with specific materials offering different benefits. For example, shiitake mushrooms thrive on hardwood sawdust, while oyster mushrooms prefer straw-based substrates. Proper preparation, including pasteurization or sterilization, is crucial to prevent contamination and promote healthy mushroom growth.
Why Is Scaling Mushroom Substrate Production Important?
Scaling mushroom substrate production is essential for meeting the growing demand for mushrooms in commercial markets. As the popularity of mushrooms continues to rise, driven by their culinary and medicinal benefits, producers must optimize their production processes to increase output and maintain consistent quality.
Efficiently scaling production involves several key factors, including sourcing high-quality raw materials, implementing automation at various stages of production, and maintaining strict quality control measures. By optimizing production processes and increasing yield per batch, commercial growers can meet market demands promptly while ensuring that their products meet the highest standards.
Moreover, adopting sustainable practices in mushroom cultivation not only benefits the environment but also aligns with consumer preferences for eco-friendly products. Scaling production in a sustainable manner ensures long-term viability and profitability in the competitive mushroom market.
How to Determine the Right Scale for Mushroom Substrate Production?
Determining the appropriate scale for mushroom substrate production requires careful consideration of several factors, including the types of mushrooms being cultivated, the chosen cultivation methods, and the availability of resources like water and space.
Mushroom Species and Substrate Requirements
Different mushroom species have unique substrate preferences and moisture requirements, which influence the scale of production. For instance, oyster mushrooms grow well on straw, which requires careful moisture management, while shiitake mushrooms thrive on hardwood sawdust, which demands specific sterilization techniques.
Understanding the needs of the mushroom species you plan to cultivate is crucial in determining the scale of substrate production. It’s important to tailor the substrate preparation process to match the specific requirements of each mushroom type to optimize growth and yield.
Cultivation Methods
The cultivation method employed—whether traditional indoor growing, vertical farming, or outdoor beds—also plays a significant role in defining the scale of production. Each method has its own set of requirements for substrate preparation, environmental control, and space utilization.
For example, indoor cultivation often requires precise control over temperature, humidity, and light, which can limit the scale of production depending on the available infrastructure. In contrast, vertical farming allows for more efficient use of space and resources, enabling larger-scale production in a controlled environment.
Resource Availability
Water usage is a critical consideration when scaling mushroom substrate production. Some mushroom species require higher humidity levels, leading to increased water consumption during the cultivation process. Efficient water management is essential to ensure that the substrate remains adequately hydrated without wasting resources.
Additionally, the availability of space for substrate production and incubation plays a key role in determining the scale of operations. Larger-scale production may require significant investment in facilities such as grow rooms, greenhouses, or controlled-environment chambers to accommodate the increased substrate volume and ensure optimal growing conditions.
What Are the Different Methods of Scaling Mushroom Substrate Production?
Several methods can be used to scale mushroom substrate production, each offering distinct advantages and challenges. The choice of method depends on factors such as the desired production volume, available resources, and the level of automation you wish to implement.
Manual Scaling
Manual scaling involves hands-on processes where every stage of substrate preparation, inoculation, and incubation is carefully managed by the grower. This method is labor-intensive but offers a high degree of control over the cultivation process.
In manual scaling, specialized equipment like spawn bags, pressure cookers for sterilization, and humidity-controlled environments are essential for successful production. Growers can adjust variables such as temperature, humidity, and nutrient levels with precision, ensuring that the substrate provides the ideal environment for mycelium growth.
While manual scaling allows for meticulous attention to detail, it may not be suitable for large-scale production due to the significant time and labor required. However, it is an excellent method for small to medium-scale operations that prioritize quality and artisanal cultivation techniques.
Semi-Automated Scaling
Semi-automated scaling combines manual intervention with automated systems to streamline the cultivation process. This method balances the expertise of human operators with the efficiency and precision of automation, making it a popular choice for growers looking to increase production without fully committing to a fully automated system.
Semi-automated systems typically involve automated equipment for tasks such as mixing substrates, regulating environmental conditions, and monitoring growth parameters. This reduces labor costs and minimizes human error while maintaining a high level of control over the production process.
The integration of automation in semi-automated scaling allows for greater consistency in substrate quality and mushroom yields. However, the initial investment in equipment and ongoing maintenance costs may be a consideration for smaller operations.
Fully-Automated Scaling
Fully-automated scaling represents the pinnacle of efficiency in mushroom substrate production. This method relies on advanced technology and equipment to manage every aspect of the cultivation process, from substrate preparation to harvesting.
In fully-automated systems, sophisticated equipment monitors and regulates critical environmental factors such as temperature, humidity, and CO2 levels, ensuring optimal conditions for mushroom growth. Automation also handles tasks like substrate sterilization, inoculation, and even packaging, reducing the need for manual labor and increasing production capacity.
While fully-automated scaling offers unparalleled efficiency and consistency, it requires a significant investment in technology and infrastructure. This method is best suited for large-scale commercial operations with the resources to support the upfront costs and ongoing maintenance of automated systems.
What Are the Pros and Cons of Each Scaling Method?
Each scaling method in mushroom substrate production comes with its own set of advantages and drawbacks, depending on the level of control, efficiency, and investment required.
Manual Scaling
Pros: Manual scaling offers hands-on control over the entire cultivation process, allowing growers to make precise adjustments to substrate preparation and environmental conditions. This method is ideal for small to medium-scale operations that value quality and artisanal production techniques.
Cons: The labor-intensive nature of manual scaling limits its scalability, making it challenging to meet high production demands. Additionally, the reliance on manual processes increases the risk of human error, which can impact substrate quality and mushroom yields.
Semi-Automated Scaling
Pros: Semi-automated scaling strikes a balance between manual control and automated efficiency. This method reduces labor costs and improves consistency in substrate production, making it suitable for medium to large-scale operations. The integration of automation also enhances the precision of environmental controls, leading to higher yields and better-quality mushrooms.
Cons: The initial investment in automated equipment can be a barrier for smaller growers. Additionally, the need for ongoing maintenance and potential technical issues with automated systems may require specialized knowledge and resources.
Fully-Automated Scaling
Pros: Fully-automated scaling maximizes efficiency and production capacity, making it ideal for large-scale commercial operations. The advanced technology used in these systems ensures consistent substrate quality and optimal growing conditions, leading to high yields and profitability.
Cons: The significant upfront investment in equipment and technology can be prohibitive for smaller operations. Additionally, the reliance on automation may reduce the level of hands-on control, potentially impacting the ability to respond to unexpected issues in the production process.
What Are the Equipment and Supplies Needed for Scaling Mushroom Substrate Production?
Scaling mushroom substrate production requires a range of equipment and supplies to ensure efficient and consistent production. These tools and materials are essential for maintaining optimal growing conditions and achieving high yields.
Sterilization Equipment
Sterilization equipment is vital for maintaining a clean and contaminant-free environment during substrate preparation. This includes pressure cookers for small-scale operations, autoclaves for medium to large-scale production, and chemical disinfectants for sterilizing tools and surfaces.
Proper sterilization ensures that harmful pathogens and spores are eliminated from the substrate, reducing the risk of contamination and promoting healthy mycelium growth. Investing in high-quality sterilization equipment is crucial for maintaining the integrity of the production process.
Substrate Mixing Equipment
Substrate mixing equipment plays a critical role in achieving a uniform mixture of substrate materials, which is essential for consistent mycelium colonization. This equipment ensures that moisture content is evenly distributed throughout the substrate, preventing pockets of dryness or excess moisture that could hinder mushroom growth.
Mixing equipment ranges from manual mixers for small-scale operations to automated mixing systems for larger-scale production. Properly mixed substrate promotes healthy mycelium growth and increases the overall efficiency of the cultivation process.
Incubation Chambers
Incubation chambers provide a controlled environment for the growth and development of mushroom substrate. These chambers regulate temperature, humidity, and airflow to create optimal conditions for mycelium colonization and mushroom fruiting.
Incubation chambers are available in various sizes, from small cabinets for hobbyists to large walk-in units for commercial operations. The ability to control environmental factors within these chambers ensures consistent and predictable mushroom production year-round.
Packaging Equipment
Packaging equipment is essential for preparing mushroom substrate for market distribution. This equipment includes machines for filling bags or containers with substrate, sealing and labeling, and adding any necessary additives.
Efficient packaging systems help maintain the quality of the substrate during storage and transport, ensuring that it reaches the market in optimal condition. Proper packaging also extends the shelf life of the substrate, reducing waste and improving profitability.
What Are the Safety Precautions to Take When Scaling Mushroom Substrate Production?
Ensuring safety in mushroom substrate production is critical to protecting personnel, maintaining product quality, and complying with regulations. Proper safety protocols must be implemented at every stage of the production process.
Equipment Safety
Equipment safety involves following manufacturer guidelines for the operation and maintenance of all machinery used in substrate production. This includes wearing appropriate personal protective equipment (PPE), such as gloves, goggles, and masks, to prevent exposure to harmful chemicals and contaminants.
Regular maintenance checks are essential to ensure that equipment is functioning correctly and to prevent accidents. Operators should be trained in the safe use of machinery and should follow all safety procedures to minimize the risk of injury.
Hygiene Practices
Hygiene practices are crucial in preventing contamination during substrate preparation and handling. All personnel should follow strict hygiene protocols, including washing hands before and after handling substrate, using disinfectants on tools and surfaces, and avoiding cross-contamination between different batches of substrate.
Proper labeling and storage of materials help prevent mix-ups and ensure that substrates are used within their optimal time frames. Maintaining a clean and organized workspace reduces the risk of contamination and promotes a safe working environment.
Environmental Control
Environmental control is necessary to maintain the optimal conditions for mushroom growth while minimizing potential hazards. This includes monitoring temperature, humidity, and airflow within the growing area to prevent the buildup of harmful gases or excessive moisture.
Proper ventilation systems should be installed to ensure a constant supply of fresh air and to prevent the accumulation of CO2 or other gases that could pose a risk to both the mushrooms and the workers. Environmental monitoring equipment should be regularly calibrated to ensure accurate readings and effective control.
Frequently Asked Questions
What is mushroom substrate production and why is it important for commercial use?
Mushroom substrate production is the process of preparing a nutrient-rich material on which mushrooms can grow. It is essential for commercial use because it provides a consistent and high-quality medium for mushroom cultivation, resulting in higher yields and profitability.
What factors should be considered when scaling mushroom substrate production for commercial use?
Important factors include the type and quantity of mushrooms being grown, the available space and resources, the chosen cultivation methods, and the market demand for mushrooms.
How can I increase the yield of my mushroom substrate production for commercial use?
To increase yield, use high-quality ingredients, maintain proper moisture and temperature levels, and implement efficient harvesting and packaging methods. Regularly monitor and adjust growing conditions to optimize production.
What are some common challenges faced when scaling mushroom substrate production for commercial use?
Challenges include maintaining consistent quality, managing contamination risks, meeting fluctuating market demands, and investing in the necessary infrastructure and equipment.
What are the benefits of using automated systems for scaling mushroom substrate production?
Automated systems enhance production efficiency, reduce labor costs, improve consistency in substrate quality, and allow for precise control over environmental conditions, leading to higher yields and profitability.
How can I ensure the safety and quality of my mushroom substrate production for commercial use?
Ensure safety and quality by using clean and sterile equipment, following proper hygiene practices, regularly testing the substrate for contaminants, and adhering to food safety regulations and industry standards.